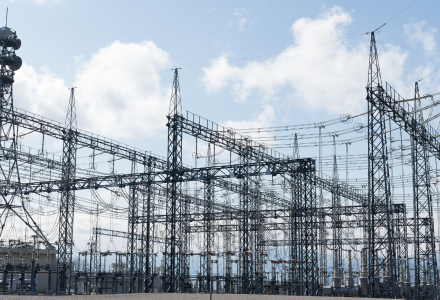
The New Hyperscale Data4Med Data Center
Client: DATA 4 MED
Services in this project:
- Technical design for architecture, structures and plants
- Safety 81/08
- Permits
- BIM Leading/Bim Management
The project involves the construction of a new Hyperscale Data Center in the former GRAFTEC industrial site, consisting of two Data Center buildings, a general office building (Customer Experience), and a disaster recovery facility.
Each building consists of three floors with data rooms and technical chambers both indoors and outside. The electrical branch gensets are located outside a dedicated GE area (genset yard). In terms of the mechanical section, the chillers are located on the roof, while internally, the rooms are cooled by Computer Room Air Handler (CRAH) systems.
Key technical data:
- 7.5 MW IT for each building, totalling approximately 3300 square metres of data rooms spread over three floors.
- For the security section, the highest standards for data centres were implemented.
- Certifications: ANSI/TIA 942-B rating IV, LEED Silver.
The BIM methodology applied in this project included the development of models for all disciplines, namely architectural, civil, fire, electrical, mechanical, security, and safety (81/08), based on the BIM Authoring Revit software.
DBA PRO. performed the BIM Lead and designer function for all the disciplines involved, including the concept design developed with BIM information modelling.
The use of BIM methodology is necessary for complex projects such as this to enable maximum multidisciplinary coordination, control of project schedules and real-time information sharing with the entire project team and key stakeholders, including the Client.
The project involved the DBA PRO. teams in the Treviso, Rome and Milan offices and entailed the creation of models in the cloud to be accessed in parallel, taking advantage of the common data environment identified for the assignment (Autodesk Construction Cloud).
All project templates and documentation have been managed, archived, and shared within the Common Data Environment (CDE), allowing all the parties involved to always have access to the latest available version of the project.
The CDE is also used to manage project issues directly within the platform. Clash handling is automated with Design Coordination features that enable automated interference checking, solution-by-solution allocation with direct reference to Revit models, and tracking associated progress (opening, management and closing).
To ensure the maximum involvement of all the parties involved in the CDE, the Client was also given access to federated models, as well as the Work In Progress (WIP) tables and added issues to streamline the exchange of information within the team and optimise all the internal design flows.
The resolution of clashes and the related control process make it possible to analyse problems and anticipate the resolution of design errors, which usually show up in the execution phase of a project. This reduces the costs associated with work stoppages, variations in progress, time extensions and related delays in the execution of works.
Given the complexity of the work, the fifth dimension (5D) was also approached, which in BIM flows makes it possible to extract the quantities of elements present in the information models in order to derive relative costs associated with list items and draw up more detailed estimated metric calculations.
For this purpose, all models were parameterised with reference to different levels of WBS in order to guarantee the traceability of the objects to extract their quantities and set up the computation through the extraction of IFC files imported into Team System CPM (IFC-compliant software) for the drafting of the estimated metric calculations for the tender.
The use of the WBS and its parameters within the information models was also exploited to set up the BIM models of safety (81/08) for the staging of the construction of the work, namely for the arrangement of the 4D flows that enabled video simulations of construction work.
This process made it possible to analyse several critical issues in the layout of the site areas (positioning of huts, cranes, etc.) and to update the safety model and related tables (which were extracted from the models) for the public tendering phase, thus guaranteeing a lower risk during the execution of the works and reducing the possibility of variations during the course of the works, which would have resulted in additional costs and associated delays on the worksite schedule.
In terms of structural modelling, all the structural reinforcing bars were modelled, which ensured the extraction of all information, detail drawings, quantities, and material lists: all directly derived from the information models, which secured the sharing of data and information.
The models were also used for communication purposes with the "Visualisation" BIM Use, to extract renders and create promotional videos. Model data were structured and organised at a parametric level to extract useful information for Quantity Take-Offs (QTO) and material definitions to support the pre-assessment for the LEED Silver certification process.
The final output involved the production of:
- graphics for the construction phase of the work, including construction details directly extracted from the models;
- documentation relating to the estimation of quantities and calculations for the definition of the construction budget;
Connect with Our Team
Project data
- Country
- Italy
- Location
- Caserta
- Year
- 2022 - ongoing
- Status
- Ongoing